Eddy Current NDT
Assessing Circumferential Cracking in Non-Ferromagnetic Heat Exchanger Tubes
Published on 21st July 2020
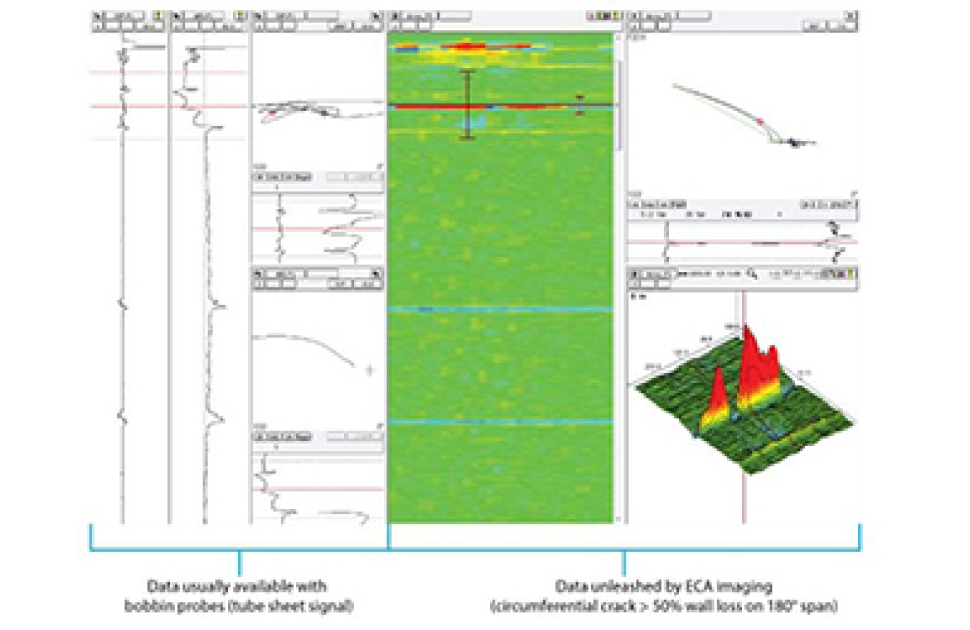
Heat exchangers are used to heat and cool various fluids in a wide spectrum of industries. This is especially critical to the power generation and petrochemical industries where the reliability of fixed equipment is paramount. Heat exchanger tubes made of austenitic stainless steel and INCONEL, for example, are plagued by circumferential cracking, which conventional, single-coil Eddy Current Testing (ECT) probes cannot reliably detect.
This application note explores how an innovative Eddy Current Array (ECA) probe technology is able to address this challenge.
The Challenge
Detecting, sizing, and positioning circumferential cracks in the vicinity of the tubesheet on non-ferromagnetic heat exchanger tubes.
Non-ferromagnetic heat exchanger tubing is susceptible to circumferential cracking in the vicinity of tubesheets. These cracks are induced by the localized stress created during the tube-totubesheet rolling process, among other things.
Circumferential cracking is very difficult to detect and characterize with standard ECT bobbin probes, currently the norm in the industry to inspect tubes, because:
- Bobbin probes are very sensitive to tube expansion and ferromagnetic materials. When analyzing bobbin coil data, it is very difficult to isolate small-volume cracks from complex signals comprised of cracks, a geometry changes, and added material.
- Standard ECT bobbin probe eddy currents flow p arallel to circumferential cracks due to the coil orientation.
Common heat exchanger components having this problem include power plant feedwater heaters and condensers, and petrochemical refinery heat exchangers. Of course, exchanger operators want to identify the tubes leaking from this issue. However, they are more interested in finding the tubes showing signs of cracks that may grow to 100% through wall while the heat exchanger is in service.
The Solution
Ectane® Test Instrument
The first is the Eddyfi® Ectane®. This tester can be configured for almost any type of inspection technique, including ECT and ECA.
Magnifi® Acquisition and Analysis Software
The second part of the solution is The Eddyfi Magnifi® acquisition and analysis software for graphical display (C-scan), record keeping, and reporting.
DefHi® ECA Tubing Probe
The final part of the solution is the patented Eddyfi DefHi® ECA probe. It leverages ECA technology to accurately detect, size, and characterize circumferential cracks, differentiating them from other unwanted signals, such as those from the tubesheet and roll transition. ECA technology uses several individual coils grouped together into one probe. The coils are excited sequentially to eliminate interference from mutual inductance (something referred to as multiplexing). So doing, coils work together to completely sweep the interior surface of each tube.
DefHi probe coils work in transmit-receive mode. They yield absolute signal responses with phase and amplitude information. Because of the coil configuration in the DefHi probe, eddy currents flowing in the tube under test are perpendicular to circumferential defects, making them easier to identify.
The Eddyfi ECA technology know-how also made it possible to optimize the distance between the transmitter and the receiver coils so the detected expansion signal is flat with respect to others, making it extremely simple to isolate. The DefHi probe is also designed to make it easy to select an optimal operating frequency for the nonferromagnetic material under test, while yielding clearly distinguishable tubesheet signals from circumferential cracking signals.
Operators can estimate the circumferential length and position of defects, something standard ECT bobbin probes cannot do.
Inspection Results
Magnifi uses the inspection data to produce 2D and 3D C-scans, which use color palettes to distinguish between tubesheets and circumferential cracks. Because the tubesheet produces an angular response with respect to defects, the latter stand out on C-scans as having depth and circumferential length, making them easy to identify and characterize. Applying an appropriate high-pass filter is then simple to completely isolate the defects.
As mentioned above, individual array coils supply amplitude and phase information. In a 2D C-scan, the ability to rotate the phase component of the signal is key to getting high-definition defect responses.
Actual testing demonstrated detection and sizing of circumferential cracks at tubesheets as early as 50% wall loss and 30% in the span area between support plates.
Benefits
Very rapid assessment of circumferential cracks in the most challenging location with full 3D imaging for easier interpretation.
Compared to standard ECT bobbin probes, the solution can discriminate between the various complex geometries inside heat exchanger tubing to allow accurately detecting, sizing, and characterizing small-volume circumferential cracks.
Compared to rotating probe technology, which scans tube ends at approximately 40 seconds per tube, The Eddyfi solution can scan tube ends at 5 seconds per tube. The DefHi probe is less sensitive to axial speed variations, so it can be used with or without a mechanical probe pushing device.
Other benefits of the solution include:
- Quantifying the circumferential extent of crack defects.
- Accurate axial location and characterization of crack defects in the vicinity of the roll transition.
- The standard ECT bobbin coil of the DefHi probe can serve as a reference point for typical ECT data signals.
- Unlike rotating probes, the solution can be used for full-length tube examinations.
- Seeing is believing
Personnel without extensive ECT data analysis experience can view the solution’s 3D data and be confident of their inspection results.
As you can see, ECA technology can greatly improve the speed and quality of results in this challenging application.