Eddy Current NDT
Detecting Flaws in Condenser Tubing Welds With the DefHi Probe
Published on 21st July 2020
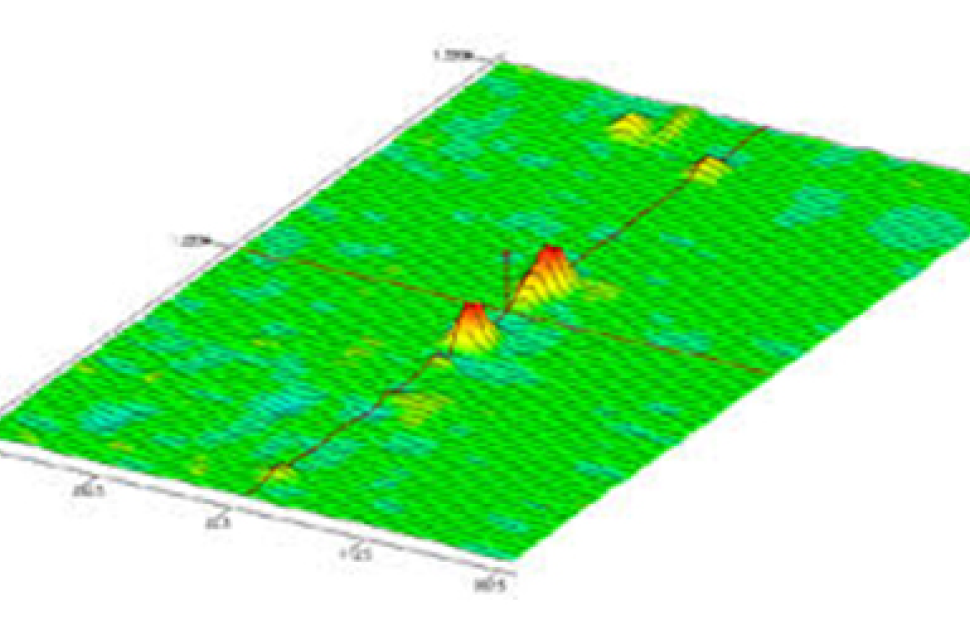
Source: https://www.eddyfi.com/en/appnote/detecting-flaws-in-condenser-tubing-welds-with-the-defhi-probe
Condensers using seam-welded tubes are usually less expensive than conventional condensers using seamless tubes. However, they can have one major weakness: the weld along the axis of the tubes.
The Challenge
Defects in the seam-welded tubing found in condensers are difficult to size and characterize.
Condensers now commonly use thinwalled, seam-welded tubes made of 304 and 316 stainless steels, as well as titanium. These tubes are susceptible to defects along weld seams—for example, axial cracking, porosity, lack of penetration, and lack of fusion.
Such defects are difficult to accurately size and characterize with standard eddy current bobbin probes because the bobbin coil yields an average response over 360° and because weld defects are only a very small percentage of the total tube wall inspected with the probe. The phase response to depth is also quite different for pits and cracks. Too often, all this leads to over sizing defects, which results in condenser tubes being plugged prematurely.
The Solution
To solve this problem, Eddyfi Technologies developed a three-part solution.
DefHi is driven by the second piece of the solution: Eddyfi® Ectane®, a test instrument designed to leverage the power of the probe.
Defect sizing accuracy becomes even more precise through Magnifi’s ability to leverage the DefHi’s array of coils. The following results are from a 304 stainless steel tube with an outside diameter of 25.4 mm (1 in) and a thickness of 0.7 mm (0.028 in). As you can see, the bobbin signals on the left of the Magnifi window can be used to compare inspections with DefHi to previous inspections performed with conventional bobbin probes.
The DefHi’s array coils show that the tube has no circumferential defects along the tube, while the axial C-scan displays several defects.
DefHi® probe
The first and perhaps most important part of this solution is the DefHi ECA probe. It is specifically designed to inspect non-ferromagnetic tubing. The probe combines ECT bobbins with the power of a multiplexed eddy current array.
The DefHi’s array coils work in a transmitter-receiver fashion and are multiplexed, yielding absolute signal responses with phase and amplitude information.
Multiplexing enables several array coils of DefHi to detect defects anywhere in tubes and allows operators to estimate the axial length and radial extent of individual defects, something that they cannot do with a standard bobbin probe.
DefHi is also designed so that an optimal operating frequency for the material under test is easy to select.
Ectane® Test Equipment
DefHi is driven by the second piece of the solution: Eddyfi® Ectane®, a test instrument designed to leverage the power of the probe.
Magnifi® Acquisition and Analysis Software
The Magnifi® software—the final part of the solution—uses all the data generated by DefHi to reduce defect sizing and characterization constraints through visual representations of the tubes (C-scans), which help operators identify defects present along weld seams.
Benefits
Reliable C-scan displays take the guesswork out of quickly locating, sizing, and characterizing defects in weld seams.
Compared to standard ECT bobbin probes, the DefHi probe can differentiate between defects occurring at the same axial location along the tube length.
Using the C-scan displays, welded tubes can be thoroughly mapped, and defects can be individually sized and characterized. In the case of weld seams, DefHi can easily display the defects as lying along the seam. Using the probe with Magnifi also enables accurately locating defects along the tube’s length.
As an additional benefit, the DefHi probe comes standard with a differential bobbin coil channel, which displays reference signals. The data from this channel can be used to compare with previous inspections where only an ECT bobbin probe was used for the inspection.
Seeing is believing—Personnel without extensive ECT data analysis experience can look at C-scan data and have confidence in the inspection results.