Visual Testing
High resolution imaging solution for the remote visual inspection of small gas turbine aircraft engines
Published on 26th July 2023
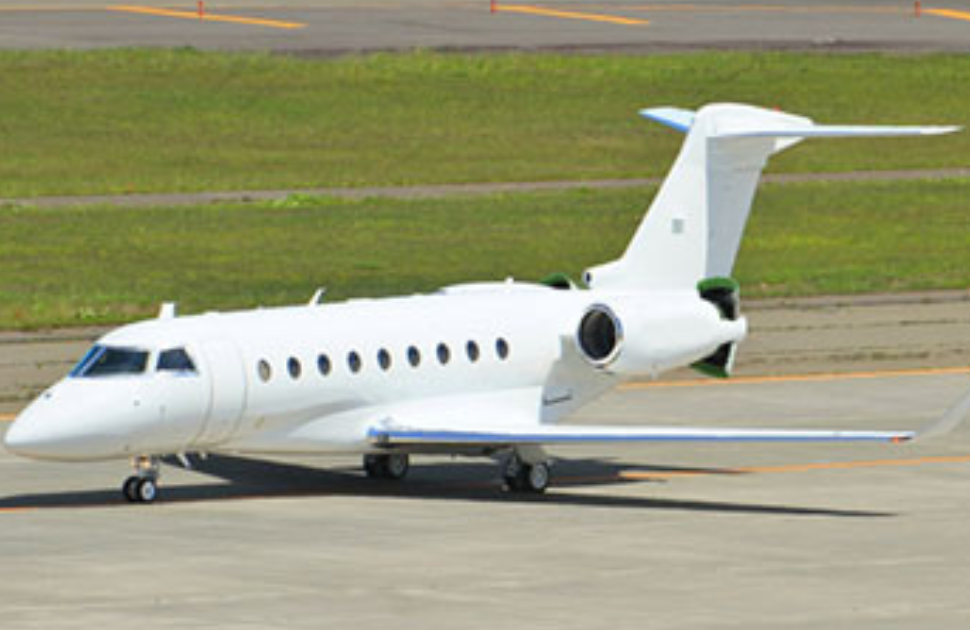
Background—Remote visual inspection of small aircraft gas turbine engines
To ensure the safe operation of an aircraft, the entire structure must be routinely and diligently inspected for damage, and a decision made on whether it should be kept in service or withdrawn for repairs. Borescope inspection (BSI) is a technique used to visually inspect the internal structure of aircraft engines. The structure of compact gas-turbine engines—used for helicopters, small aircraft, etc.—is relatively simple, so there are only a few parts to inspect. The internal components include a compressor, turbine, fuel nozzle, combustion chamber, and nozzle guide vane (NGV). Inspectors usually use a rigid scope or a fiberscope to visually examine these components. Visual inspection requires proficiency in the inspection technique to prevent any oversight. A rise in the volume and demand for small aircraft inspections has resulted in an increase in the number of new maintenance engineers. And, regardless of their lack of experience with the BSI technique, they are expected to meet the same strict inspection standards as their more proficient counterparts. The easier it is to identify damage, the better.
Solution using IPLEX industrial video scope high-resolution imaging systems
The IPLEX series of industrial video scopes feature Olympus’ exceptional image quality and application-specific accessories to assist inspectors in compact gas-turbine engine inspections:
High-resolution sensor and PulsarPic processor for crisp, vivid images
Unlike conventional borescopes or fiberscopes, video scopes display the captured images on a portable monitor. IPLEX video scopes capture images using a high-resolution solid-state image sensor at the tip of the scope. The captured data are then passed through an optimized image processor called PulsarPic and displayed with excellent clarity on the video monitor. Inspectors have a clear view of components, even those in dark, cramped spaces, making it easier to spot flaws, regardless of their level of experience.
Optical tip adaptor series that anticipates and meets various viewing needs
The insertion tube of an IPLEX video scope can be used to inspect various parts inside a gas turbine engine by replacing the optical system at its tip. For instance, compressor blades and turbine blades, located relatively near the insertion hole, can be inspected using a side-viewing adaptor with a near-focus depth of field (DOF). The larger space of the combustion chamber, on the other hand, can be inspected using a forward-viewing adaptor with a far-focus DOF. In addition, the interchangeable optical systems are fixed to the tip of the borescope with a double screw thread to hold them securely in place, helping prevent FOD-related accidents.
Left: Existing rigid scope
Right: IPLEX video scope
Left: Existing rigid scope
Right: IPLEX video scope
Removable and replaceable optical tip adaptors
Screwed on with a double thread
Benefit to the customer
The live video monitor of an IPLEX series video scope provides vivid, high-quality images of the internal components of gas-turbine engines to aircraft maintenance engineers. Through this powerful imaging technology and a range of optical tip adaptors suited to specific viewing needs, IPLEX video scopes help ensure that inspectors of all experience levels perform reliable and consistent inspections, contributing to the safe operation of small aircraft gas-turbine engines.