Pulsed Eddy Current
Mitigating the Cost of Not Knowing in Ships
Published on 24th July 2023
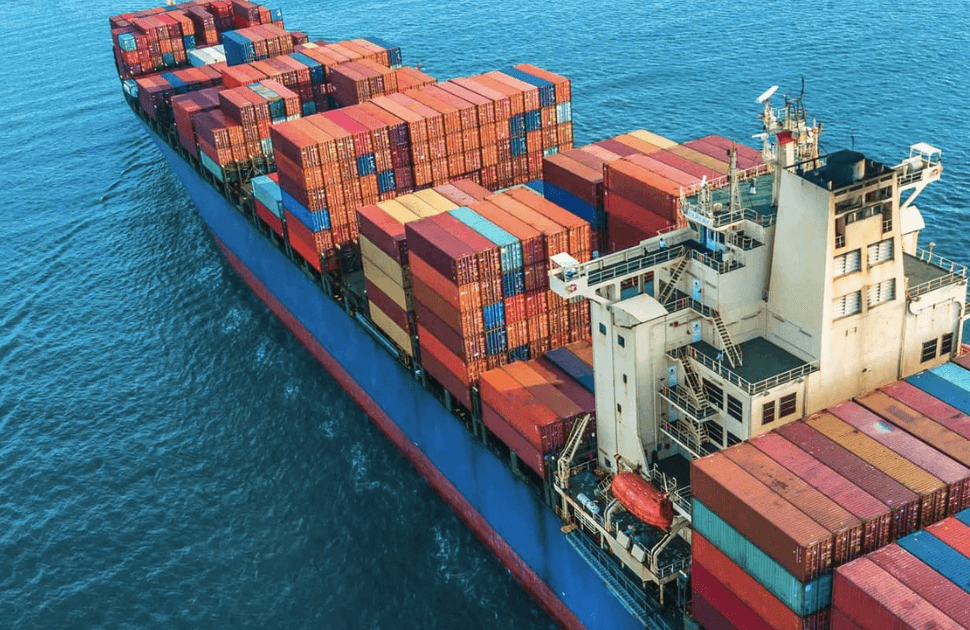
Ships are important assets for various organizations in the field of research, coast guards, and navies, to name only a few. Considering the cost of commissioning new ships, more and more operators want to extend the service life of existing assets as much as possible. For the most effective life extension programs possible, repairs must be as targeted as possible, highlighting the need to know what must be repaired before contracting repair work.
The Challenge
Map corrosion in ship deck plates quickly without removing coatings or linings.
Deck plates are essential parts of ships because they are vital to their structural integrity and the health and safety of their personnel. They are plagued by corrosion that remains unseen until it is usually too late.
The plates are lined with a non-slip epoxy coating and/or a variety of materials from ceramic tiles to concrete by way of wood that conceal corrosion. Linings must be removed before plates can be inspected to find out whether they need repair or not—very expensive and, arguably, quite destructive. Inspection/repair service providers, however, often quote jobs based on surface area, without usually knowing exactly what will actually have to be repaired. Once linings are removed and deck plates are inspected, the overall portrait of their state often drives the price up significantly. You can see that beginning work without previous knowledge of what lies underneath is a costly mistake—the cost of not knowing—hence the need for a solution that can assess this before removing anything.
The Solution
Pulsed eddy current solution enabling scans through coatings and linings.
Corroded plate used in testing
Corroded plate underside
First scan, sides clamped, along stiffeners
Second scan, no clamps, along stiffeners
Third scan, no clamps, perpendicular to stiffeners
In recent years, Eddyfi Technologies has spared no effort in evolving Pulsed Eddy Current (PEC) technology. It has the demonstrated advantage of being able to scan through non-magnetic coatings and insulation to discover the corrosion hiding underneath, without having to strip said linings.
All this research and development gave birth to the Eddyfi Lyft® PEC solution. It features a state-of-the-art portable instrument; real-time C-scan imaging; fast data acquisition (up to 15 readings per second) with grid and dynamic scanning modes.
The solution also features a range of PEC probes for a variety of applications.
In this particular application, the carbon steel deck plate extracted from a decommissioned ship and targeted for inspection was approximately 5.4 mm (0.213 in) in nominal thickness, and the lining 20.0 mm (0.787 in). The far side of the plate featured several other elements such as welds and stiffeners. Corrosion on the sides of the plate pushed the lining upward, separating it from the steel plate by close to 7 cm (2.8 in) on the left side. Bulges in the lining were also visible, the result of ferrous oxide buildups.
Considering the thickness of the deck plate, lining, and corrosion product in this application, our engineers used a small PEC probe. All our scans were performed at a grid resolution of 25 × 25 mm (1 × 1 in). For the first dynamic scan, clamps were used to close the gaps between the plate and lining.
This scan raised several questions: How will the data be affected if the left-most gap is left open? Will the stiffener signals be affected by a change in the scan-axis? How repeatable are scanned on the same plate?
To answer these questions, our engineers re-scanned the plate without the clamps to leave the gap between it and the lining open. The second scan of the plate revealed that, when compared to the first, data was not significantly affected by the gap or oxide buildup.
A third scan was performed perpendicular to the stiffeners. Based on this scan, our engineers concluded the following:
- When scanning along the stiffeners, they are visible in a 50–75 mm (2–3 in) wide line.
- When scanning perpendicularly to stiffeners, their signals are weaker but spread across a wider area.
We could therefore conclude that scanning along stiffeners will help better position them while maximizing the detection of corrosion in close proximity to them.
Similar inspections were performed on other ships with the same success, conclusively demonstrating that PEC was able to assess the presence and relative extent of corrosion in deck plates before undertaking destructive repair work.
The Benefits
Enables the efficient mapping of corrosion in deck plates, effectively mitigating the cost of not knowing.
The most important benefit derived from using PEC over lined deck plates is simple: it mitigates the cost of not knowing. Avoiding stripping and the ability of PEC to scan through the entire thickness of deck plates despite stiffeners and other landmarks enables precisely targeting areas that need repair.
PEC can help monitor the progress of corrosion over time, using stiffeners as landmarks, and ignoring welds and studs (because they do not affect PEC inspection results). This translates into a better understanding of corrosion mechanisms in deck plates, and therefore more efficient repair operations.
In the short and long runs, being able to see corrosion and its extent offers enormous budgetary savings and helps avoid potentially catastrophic failures. (Simply look up “ship failure corrosion” in Google Images).
As you can see, PEC technology helps you quickly assess the structural integrity of components prone to corrosion without having to remove what’s hiding it, first.