Others
Pressure Decay and Leak Testing Essentials
Published on 21st September 2020
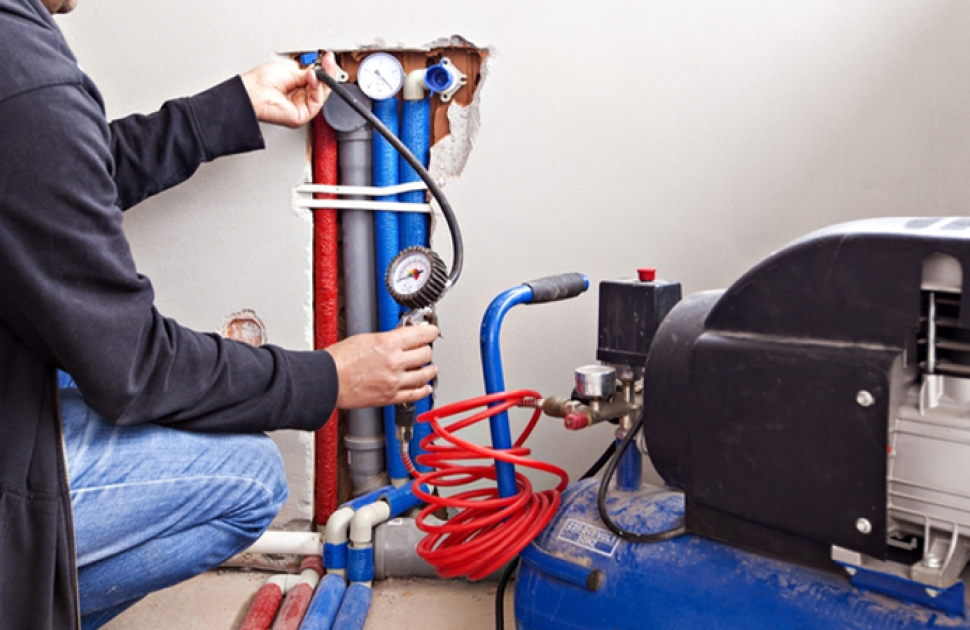
In its simplest terms, pressure decay leak testing fills a vessel with
air and then measures the loss of the pressure over a set period of time. If
the pressure drops it indicates a leak. The speed at which this occurs – the
decay – is used to determine the extent of the leak.
Although this type of leak testing has been around for a long time, it’s still in common use and is popular, thanks to the ease of use and highly accurate results. You might also see the method referred to as ‘vacuum decay testing’.
Pressure decay leak testing works in the following manner:
- The internal volume of the item or asset to be tested is calculated.
- Space is pressurized before being isolated from the source of the pressure.
- This pressure is then monitored over a pre-defined length of time.
- Any loss in pressure indicates a leak. By computing the rate of pressure loss, the size of the leak is easily determined.
- In general, the larger the vessel, the longer the cycle time will take.
There are two methods of measuring leaks using pressure decay. These are:
- A differential pressure transmitter: This is the faster of the methods and is the more sensitive of the two.
- A gauge-type transducer: Slower than the above, it’s still very effective at the detection of very small to small leaks.
Benefits of pressure decay leak testing
Besides being an accurate and inexpensive method of testing, pressure decay offers the following advantages:
- Can be used to test in pressure or vacuum environments
- Highly sensitive to even the smallest of leaks
- Simple and effective
- Can calibrate to a volumetric flow
- Reports both flow and pressure loss
- Produces quantifiable results
- Can be easily automated
- Well suited in situations that demand validated test protocols, such as medical devices and in the automotive industry
· Another method of industrial leak testing is that of helium ion testing. Compared with pressure decay testing it’s a more complicated, costly process, and one that’s not as easily automated, making the vacuum/pressure method a more popular alternative in many situations.
· Acoustic leak detection uses special microphones to detect sounds produced by gas that escapes through small leaks. This is especially effective for the detection of leaks at long distance, and often used in the oil and gas industry, and for deep water pipes.
· Other methods include laser technology and hydrostatic testing.
Whatever method is chosen to test for leaks it’s important to determine the most accurate solution for a particular situation. Pressure decay leak testing remains a cost-effective option in many applications, being easy to implement, returning highly accurate and recordable results, plus the ease in which it can be automated makes the procedure a valuable asset in multiple industrial contexts.
Determining the correct solution for asset testing is a key aspect of why leading equipment supplier, Nexxis, are fast becoming the go-to source for a wide variety of industry specialists. With wide-reaching expertise in industries such as the oil and gas, mining, sub-sea and manufacturing, the team understands the ever-changing requirements of today’s dynamic environments.
To this end, their professional team partners with their customers to provide the vital flexible solutions necessary for companies to remain current and competitive in their particular field.
To discover how this refreshing approach to equipment solutions can give
your business the edge, call