Eddy Current Testing
Robotizing Eddy Current Array to Find Stress Corrosion Cracks in Stainless Steel Canisters
Published on 26th May 2020
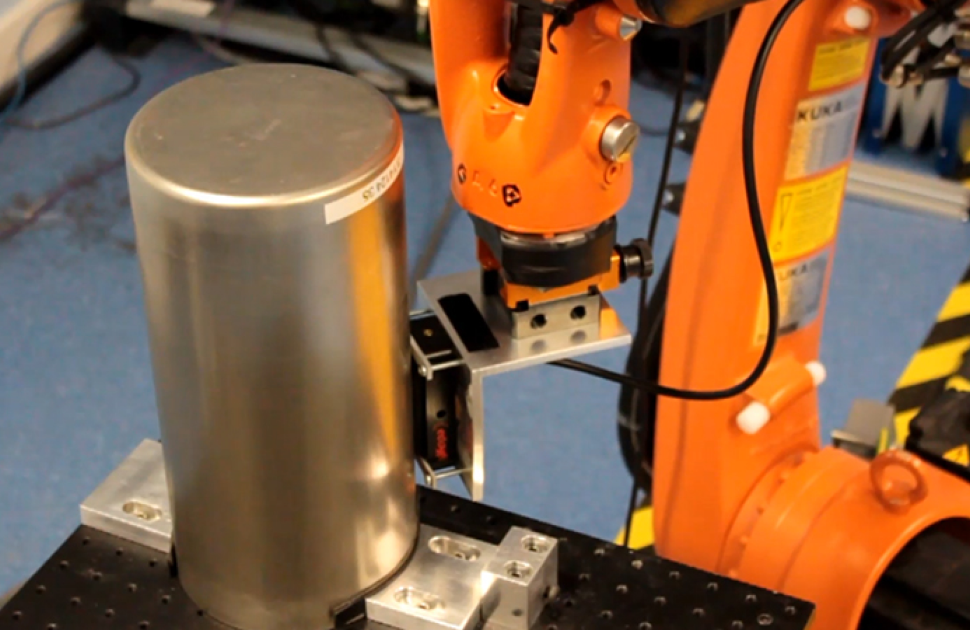
Eddy Current Array (ECA), more so than most other inspection
techniques, has proven an adaptable, powerful, and cost-effective
technology, and therefore very well suited to robotization.
This note focuses on one such application: scanning stainless steel canisters used in the containment of nuclear material for long-term storage.
- Robotize a reliable NDT technology to detect AISCC in stainless steel canisters used to store nuclear material.
These stainless steel canisters are stored by the thousands and they require periodic inspection because they may develop signs of Atmospherically-Induced Stress-Corrosion Cracking (AISCC). The inspection of such containers poses a significant challenge due to the large quantities involved; therefore, automating the inspection process is of considerable interest.
Particle deposits on the canisters absorb air moisture, forming a thin layer of concentrated salt solution that may cause AISCC if there is enough residual stress in the canister. The salt solution may also cause pitting, but the application is primarily concerned with AISCC.
The challenge of this application is to robotize an inspection solution capable of detecting stress-corrosion cracks ranging from hundreds of micrometres to 2–3 mm (0.08–0.12 in) in length.
A canister was prepared to test the solution with 16 crack-like defects. Since the AISCC defects were positioned on only one vertical half of the canister, the horizontal extent of the inspection was limited to 180° (in angular terms).
The Solution
- ECA probe with a padded scan interface mounted onto a low-payload robotic arm scanning canisters in a vertical raster scan.
Electromagnetic testing has a longstanding record of reliability on materials such as stainless steel for detecting surface and near-surface crack defects such as AISCC. ECAimproves on conventional eddy current testing in the following ways:
- ECA arranges several coils in rows, which yields a wider inspection area.
- ECA coils are excited in elaborate sequences to strike a balance between the minimal mutual inductance between coils and the maximum array resolution.
- ECA probes are more stable than conventional pencil probes, and offer a higher tolerance to variable coupling, making them better suited to robotization.
The ECA probe used here contains 32 coils, 2 mm (0.08 in) in diameter arranged in two rows. The probe has an operating frequency range of 100–800 kHz, a coverage of 54 mm (3.74 in), and a highly resistant padded scan interface, which are perfect for singlepass scans. The probe was mounted on a KUKA KR 5 low-payload robot controlled through a KR C2 unit. The KUKA|prc (parametric robot control) was used to program the scan path. Mounting the ECA probe 90° with respect to the robot’s wrist produced a path where the joint angles of the robot were well within its operating range. The inspection solution is driven by the Eddyfi® Ectane® test instrument at 400 kHz. A visualization module was written to take the eight C-scans (transverse and axial) from the four raster passes produced by the Eddyfi Magnifi® acquisition and analysis software, and project them onto the surface of a half cylinder; this was the final output of the system. The solution was able to detect most of the simulated surface cracks on the test canister in approximately 60s, but the final ECA probe will be selected according to the range of defect sizes to be detected in the field.
Benefits
- An easily robotized, rugged solution capable of detecting AISCC in stainless steel with reliable, repeatable results, and requiring no surface preparation.
An ECA solution offers a number of benefits to robotization: