Eddy Current NDT
The Fast and Reliable Alternative for Orbital Weld Inspection: Eddy Current Array.
Published on 1st July 2023
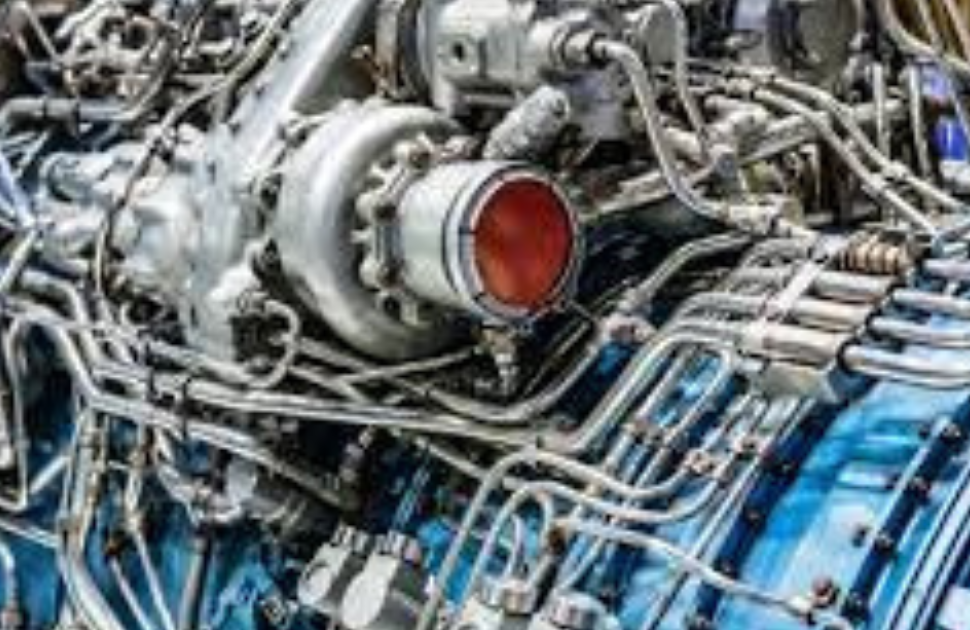
Image credit @eddyfi
Orbital welding is a widespread process used in the aerospace industry to produce high-quality joints in fuel lines, brake lines, and hydraulic lines, among other applications. The integrity of these welds is critical; a small defect could cause a leak and pose a major safety issue. To ensure the reliability of rockets and aircraft, non-destructive inspection is used to ensure the quality of the joint and prevent weld failure. Currently, penetrant testing and radiography are the most widespread methods used to conduct this non-destructive inspection. However, it can require up to one hour for a single weld. With hundreds of orbital welds in an aircraft, this inspection can become intensive in both time and resources. Radiography can also be difficult to deploy due to the safety zone requirements and the limited space around the tubes. This demonstrated the need to develop an alternative non-destructive testing method that would meet the detection performance required for orbital welds while drastically reducing the inspection time. To tackle the multiple challenges involved, the team at Eddyfi Technologies is proud to present a new and more economically viable solution based on Eddy's current array.
The Challenge
The inspection of orbital welds is highly time-consuming and calls for a more efficient method of non-destructive examination.
Orbital welding was developed in the 1960s to prevent leakage issues from hydraulic and fuel systems. These tubes are usually small in diameter and are located in areas with restricted access, which makes manual welding difficult and unreliable. Instead, orbital welding is an automatic process that produces a high-quality tungsten inert gas, or TIG, weld and is now widely used in aircraft and rockets. But even with a highly controlled welding process, defects such as small cracks and porosities can still be present in the joint. Over time, these defects can propagate and lead to fuel leakage, thus endangering the safety of commercial aircraft and potentially causing propulsion system failure in rockets. The current inspection procedures involve penetrant testing combined with radiography, which yields good detection performance and reliability. However, because it can take up to one hour to inspect a single orbital weld, this technique is costly and time-consuming.
In itself, the inspection of orbital welds presents several challenges. First, a lot of fuel lines have a diameter as small as 6 millimeters (0.25 inches) with very thin walls of less than 1 millimeter (0.04 inches). Orbital welds can also be hard to reach or located in a confined area. Finally, even small defects like porosities can compromise the integrity of the welds and need to be detected at an early stage.
The Solution
A custom eddy current array probe that clamps around the orbital weld was designed for high-resolution inspection.
To tackle this challenge, Eddyfi Technologies worked with multiple aerospace companies to develop a custom eddy current array probe that is designed specifically for the inspection of orbital welds. The probe consists of a mechanical clamp that attaches to a tube. Inside the probe, an array of small high-resolution coil sensors ensures proper coverage of the weld, while maximizing the resolution. An encoder is embedded in the probe to facilitate the circumferential positioning and length sizing of the defects. The probe is designed to be rotated manually around the orbital weld in an encircling motion. This guarantees good contact between the sensors and the surface while allowing the inspection of the whole circumference in a single pass. This design makes the inspection repeatable, operator independent, and much faster than inspecting the same weld using penetrant testing and radiography. The whole inspection process with an eddy current array only takes a few minutes. The size of the probe was also minimized to ensure its successful deployment in restricted spaces.
The first image below shows the C-scan indication of a transverse crack 2 millimeters (0.080 inches) long by 0.2 millimeters (0.008 inches) deep. The second figure shows the indication of a cluster of porosities. A detection gate with an adjusted threshold helps to identify the defects without requiring manual data analysis.
Small Crack
Cluster of Porosities
The results show a high Signal-to-Noise Ratio (SNR) which leads to reliable detection, even for small clusters of porosities. Using Eddyfi Magnifi® acquisition and analysis software, the defects can be automatically tagged based on an adjustable signal threshold. Advanced data analysis tools such as filters can help reduce the level of noise, further improving the SNR.
The Benefits
The developed solution makes it possible to reliably detect small inner and outer cracks and porosities within only a few minutes.
The eddy current array system designed by the team at Eddyfi Technologies makes it possible to inspect and analyze the data of an orbital weld within minutes. It has proven able to detect small inner and outer cracks as well as clusters of porosities. It's custom mechanical design ensures that the inspection is fast and repeatable. Thanks to the Magnifi software, data is easily visualized and recorded while making the defect identification operator independent.
Compared to visual inspection and radiography, Eddyfi Technologies' eddy current array solution saves both time and money by reducing tenfold the time required to conduct the inspection of orbital welds. For more information, Contact US today.