.png)
Advanced fatigue analysis of offshore jacket tubular joints
This webinar is relevant for structural and offshore engineers, group leaders, engineering managers, and technical authorities responsible for the design and re-qualification of fixed offshore assets intended for use in the offshore wind or oil and gas segment.
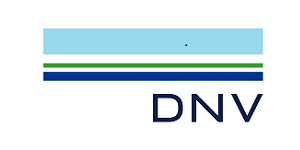
Learn how to convert tubular joints to FE models for refined SCF calculations or shell fatigue analysis.
The re-analysis of an asset after many years in service may show that fatigue life has been passed or is close to end of life. This could be a showstopper for re-qualification, as it may be too expensive to strengthen the joints. Fatigue analysis using refined SCF (stress concentration factor) or shell elements may give less conservative fatigue life. This is beneficial during the design of a new asset for use as a foundation for offshore wind turbines or traditional oil and gas.
Watch this webinar recording to discover when, why and how to convert tubular joints and create a shell finite element model using Sesam.
Agenda:
- The principles behind Sesam’s automatic conversion of tubular joints and finite element settings to support DNV GL RP-C203
- How to convert different types of tubular joints to shell models
- How to add local stiffeners to a tubular joint shell model
- How to streamline the analysis workflow to do fatigue analysis of shell models
- Case study comparing the fatigue lives from pure beam model and shell model integrated with global model
- Sesam - Fatigue of tubular shell joints
The webinar video is relevant for:
Structural and offshore engineers, group leaders, engineering managers, and technical authorities responsible for the design and re-qualification of fixed offshore assets intended for use in the offshore wind or oil and gas segment.
Why watch?
If you need to demonstrate improved fatigue life of new and ageing assets, this webinar will help you to become more efficient when:
- Converting tubular joints to shell models to calculate refined SCF
- Performing dynamic analysis to use in shell fatigue.
Watch the demonstration and witness how the time spent in conversion work is reduced from days to a couple of minutes.
If you are currently using Sesam, this webinar will help you to get the most out of your license. If you are working with other software, this webinar will shed light on a methodology that can help you gain efficiency and reduce costs.
Presenter
Ole Jan Nekstad, Product Director for Sesam, took his M.Sc. in offshore engineering from NTH (now NTNU), Trondheim, Norway in 1981. He has since then worked for DNV and has done numerous FE analyses of ships, semi-submersibles, GBS and jackets. He joined the software part of DNV in 1989 and has since 1994 been looking after Sesam as its product director. He was project manager of the JIP “Sesam 2000” that lead to the Sesam as of today.