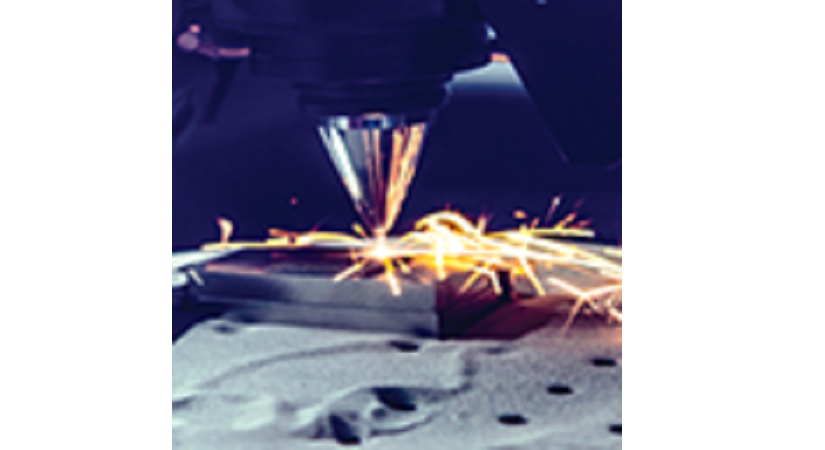
Nondestructive Evaluation for Metal Additive Manufacture
Progress in Nondestructive Evaluation for Metal Additive Manufacture via X-Ray Computed Tomography: A USAF Perspective
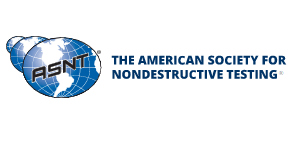
X-Ray computed tomography (XCT) is the most frequently used nondestructive method for evaluating metal additive manufactured (AM) components. Expected takeaways from this presentation include:
- Limitations for common NDE/NDT methods for analysis of metal AM
- Why XCT is the most often used modality for the NDE of metal AM
- The current limitations of XCT for defect detection in metal AM
- Areas for improvement for XCT as the NDE method of choice for metal AM
- Use of microfocus XCT imaging to characterize internal porosity in an AM sample
Based on a literature survey of the implementation of nondestructive evaluation (NDE) methods for metal additive manufacturing, this webinar explores the advantages and disadvantages of commonly used methods before delving in depth into XCT. A correlative characterization of internal porosity in a 10 mm diameter Ti-6Al-4V (Ti64) additively manufactured sample is provided. An XCT reconstruction is compared to a mechanical polishing-based serial sectioning (SS) reconstruction over the same volumetric region. Microfocus XCT imaging was conducted to characterize the internal porosity within the sample, at a voxel resolution of approximately 23 microns. After XCT imaging, SS was used with optical microscopy characterization at a much finer spatial resolution—approximately 22 ×— and compared to the XCT reconstruction. The quantitative results of stereology, area fraction of porosity, and equivalent pore diameters are presented. The comparative results for manual data registration are also presented, as well as the future direction of research resulting from this current study.
CONTRIBUTORS
Bryce Jolley has worked for 16 years for the Department of Defense as a process engineer, materials engineer, and research engineer. The majority of that time has been in a laboratory setting. Bryce obtained his Bachelor’s from Utah State University and his Master’s from the University of Utah where he is also pursuing his Ph.D. For the last six years Bryce has been immersed in the world of NDI/NDE/NDT first while serving as a laboratory director required to oversee all NDI Level III activities at Hill Air Force Base in Utah and now as a researcher trying to figure out best practices, principles, and guidelines for the NDE of metal additive manufacture. Bryce is married and a father to three growing boys that devour everything in sight to include his non-working time.